What is modular construction and is it the future of the construction industry?
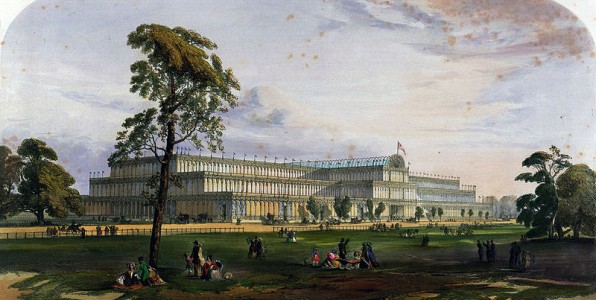
What is modular construction and is it the future of the construction industry?
The construction industry is under repair, and it is changing drastically. With housing demands continuously growing, the construction industry is facing some huge hurdles. One of the biggest challenges is that the once-efficient building methods won’t create structures quickly enough.
Construction methods require a much-needed upgrade, especially with the growing skills shortage, and this has led to a turning point in the industry. While modular construction isn’t technically new – it has been around in some form since the 1830s – it is seeing a revival thanks to its efficiency and cost-effectiveness.
What is modular construction?
Modular construction, also known as prefabricated construction, is the process of creating the components that will make up a building off-site, often in a factory. These are then transported to the site where they are assembled, saving time digging, bricklaying and more.
Because of its efficiency, modular construction is being used more and more over recent years. This isn’t limited to homes, either. Prefabricated buildings also house restaurants, hotels and hospitality locations, among others.
It’s easy to see why modular construction becomes so popular during a housing crisis. The quick process enabled a housing boom in Britain after World War II until the somewhat utilitarian design saw it fall out of style.
But it was around over 100 years before this. The first documented prefabricated home was built in England in the 1830s before being shipped to Australia for assembly. The method then made its way across the pond to the United States in the 1840s to accommodate housing needs during the California Gold Rush.
Perhaps the most famous example, however, was Crystal Palace in London, constructed for the Great Exhibition in 1851. Made of iron, wood and glass, it only took a few months to build and after its use, it was dismantled, moved and reassembled elsewhere.

Image source: Wikipedia
The types of modular construction
There are two different types of modular construction. Both have their own benefits and provide different features for the specific needs.
Permanent modular construction
As it says in the name, this form of modular construction is built to stay. It is made to be durable and safe, its longevity means it remains standing until it’s demolished.
The innovative, sustainable method is created with prefabricated materials to provide standalone buildings or provide as a solution for homes, flats and other integral buildings.
Relocatable buildings
This method is used for temporary buildings, but it doesn’t scrimp on safety. All relocatable prefabs still have to comply with the regulations of usable buildings, but they have the added benefit of being able to be deconstructed and moved elsewhere.
Structures such as schools, medical clinics and construction site offices are often manufactured in this way to provide fast-action, easily accessible buildings that meet immediate needs. When the buildings are no longer needed, they can be broken down and relocated elsewhere.
9 benefits of modular construction
Now that we know what modular construction is and how it can be used, what are the benefits? Why are so many construction firms now turning to it for the projects?
- It’s helping solve the UK brick shortage
In 2020, there’s an unlikely problem in the construction industry: a shortage of bricks. It’s an issue that isn’t going away, with current research showing that there are companies having to wait over a year on average. It has been revealed by the Federation of Master Builders that bricks have both the longest wait time, and rake up the highest prices, that have recently increased by 9%, due to the raw materials used to make each individual one. This is killing potential client deals and projects, causing many to lose vital revenue due to the increasing wholesale price of brick.
The deficit rose from the 2008 recession when money was short, and the housing market faced a significant decline. Because of this, brick companies were hit the worst. To try and stay afloat, the brick industry had to make developments much more expensive for it to be worth both time and money.
Modular construction has become a lifesaver. Instead of bricks, buildings are made from wood, concrete and steel. This keeps costs down and reduces waiting times for materials.
- It’s environmentally friendly
Green construction is on the up. Eco-friendly projects save money for construction firms and clients, making them very attractive. Modular buildings are a part of this.
By being created off-site in factories, construction waste is dramatically reduced as the materials can be easily recycled. In fact, leftover wood, steel and concrete are often used to make other prefabricated building parts.
This construction method also limits hazardous waste, and it helps prevent pollution of the area around the building site. If you want to maintain a good reputation with the locals, modular construction will help you out.
- There’s less site disruption
Supply chains are complex – especially in construction. Every material could come from a different supplier in a different country, causing a headache for supply chain management. Delays are common, and could be due to the weather, transport links like ferries and even the geopolitics in your supplier’s location.
Having buildings made almost entirely in a factory, supplies are only coming from one location. There are no more delays, which means no more worrying about breaching contracts and having to pay compensation. Suddenly, the construction supply chain is simplified.
Not only this, but it also takes away a small fragment of the traditional disruptions that a construction site can come across. Delivery noise from trucks, skips and large cranes will be significantly reduced, along with other irritants like waste and local pollution.
- There’s better labour efficiency
Taking work off-site and into a factory doesn’t just benefit the environment – it also helps with labour costs. Repetitive on-site jobs like bricklaying are replaced with the automated construction of prefabricated pieces, saving firms time and money.
Thanks to this, workers can focus on smaller, more technical tasks, and complete them quicker than before. They can also take the time to upskill and learn new techniques, helping to move the construction industry forward and combat the skills shortage.
- You can use durable materials
We all know that bricks last. In fact, the International Association of Certified Home Inspectors claim that brick buildings are made to last for over 100 years. But the rumours around prefabricated buildings being insubstantial are completely unfounded.
Modular construction doesn’t cut back on quality – it uses high-quality, durable materials to create safe, durable structures.
Indeed, it opens the door for other materials to be used, each bringing their own benefits. Concrete helps with acoustics and thermal insulation while also being able to withstand natural disasters like earthquakes and hurricanes. It even comes with the added advantage of being able to be recycled into pavements at the end of the building’s life cycle. Meanwhile wood is naturally resistant to electrical conduction and slate will look attractive for over a century.
With modular construction, it’s likely that a house will waste less energy and even be somewhat fireproof. Money and lives can be saved, just by using something other than brick.
- It poses less danger to workers
With the majority of the work taking place in a factory, the health and safety of on-site construction workers can dramatically improve. Instead of heavy machinery lifting dangerous objects overhead, building components are already made when they arrive at the site – all that’s left to do is assemble.
Risk assessments become much simpler. Work at height is significantly reduced along with the risks of slips and falls. The lack of noise will also help to lessen hearing problems and disruption.
- It’s quicker
Buildings take a long time to construct. From digging the foundations to laying each individual brick, it’s a lengthy, expensive process.
Not with modular construction. These projects are typically finished 30-50% quicker than with traditional methods because foundations can be dug while the components are being built off-site. This means more projects can be completed, bringing in more revenue for construction firms.
- There’s customisation freedom
Due to being made in a factory, the processes and materials from conducting modular construction allows that of a customisable element for better aesthetic innovation.
This separates modular construction from traditional methods, as the latter designs are usually restricted to how inventive they can be due to restrictions on shape, size and specific regulations in local areas. However, with the ability to create in any shape or form, modular construction can adapt itself to certain regulations without risking size, aesthetic or durability.
Through modular building, every element can be tailored to exactly what is asked for, meeting budget, design and user requirements. This creates economically friendly new builds – a much better investment for those purchasing a new home, as well as the construction industry.
- There’s more freedom in location
Trying to build in a tight spot with limited access can be incredibly difficult. Logistics becomes a nightmare, and large machinery may struggle to get on-site.
Modular construction removes that problem. Sites no longer need bulky machines and a considerable number of workers. Instead, few vehicles have to travel to the site, minimising logistical issues and disruption.
Solving the housing shortage
With the world’s population growing faster than ever and the housing industry being unable to keep up with demand, modular construction could be the answer we’ve been looking for. House prices are skyrocketing, and workers on minimum wage find it hard to pay their rent, let alone put together a downpayment for a house.
Modular construction could have the power to change this. By making house construction much cheaper without sacrificing quality, house prices could decrease, revolutionising the market and putting a roof over more heads.
The quick turnaround time would be a boon here, too. A house could go from planning to moving day in just six months.
The drawbacks of modular construction
No building method provides the perfect solution to the industry’s problems, and this certainly holds true for modular construction. While it has a plethora of advantages, it does have its limitations.
While size is theoretically no issue when it comes to prefabrication, the reality is very different. Transportation limits how big individual pieces can be, consequently putting limitations on designs and logistics.
At the same time, through no fault of its own, modular construction has gained a bad reputation. A lot of stigma surrounds the quality of prefabricated buildings, with many arguing that they’re not strong or durable. This has the knock-on effect of reducing resale value.
Of course, this could change as modular construction evolves and becomes more mainstream, but for now, it definitely has a negative impact.
Summary
The future of the construction industry is up in the air at the moment – the coronavirus pandemic hasn’t helped with this. But will modular construction have a part in its future?
Bricks and mortar have proved their longevity, but so has prefabrication without people realising. Many ‘temporary’ buildings constructed after World War II are still standing, and we now have the power to improve on them.
Some experts are predicting that we’ll see a 6% increase in modular construction by 2022 and it is thought that the modular construction market would expand to $130 billion in 2030, but it’s currently hard to see if the pandemic is changing this figure. What we can take comfort in, though, is the fact that 84% of Sweden’s new detached homes use prefabricated timber elements.
With modular construction, we have a blank canvas to make environmentally friendly, attractive buildings at a fraction of the cost. We can erect homes, schools, hospitals, hotels and more on short timescales that will last lifetimes.
Only time will tell if the industry is able to make a move in this direction. But there’s no denying that modular construction has the power to transform the sector and people’s lives in 2021 and beyond.
Comments are closed