How to deliver true low carbon housing for the planet
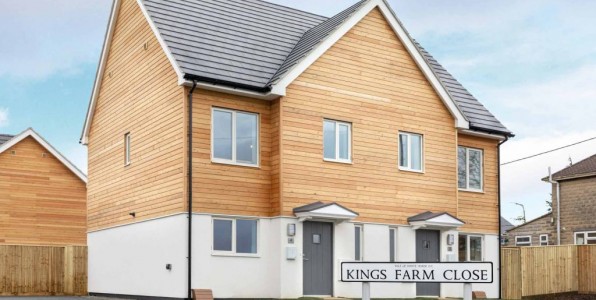
How to deliver true low carbon housing for the planet
In its 2019 Spring Statement the government
said it will aim to end the use of fossil fuel-based heating systems in all new
homes from 2025. It’s a bold move, and one that certainly brings even more
focus on improving the sustainability credentials of the UK’s new-build housing
stock. But what else should be done to make our homes truly low carbon and
sustainable?
Going beyond operational efficiency
In the quest to reduce CO2
emissions and produce ‘nearly zero-carbon buildings’, most designers and
builders focus on lowering operational emissions – even if it means emitting
more CO2 in the construction process. There’s still very little
thought put into reducing the CO2 emitted during the build stage and
from the materials used in the building fabric itself.
There are, however, pockets of developments
appearing across the UK – built by innovative SME builders harbouring a social
conscience – that take a more holistic approach to sustainable housebuilding.
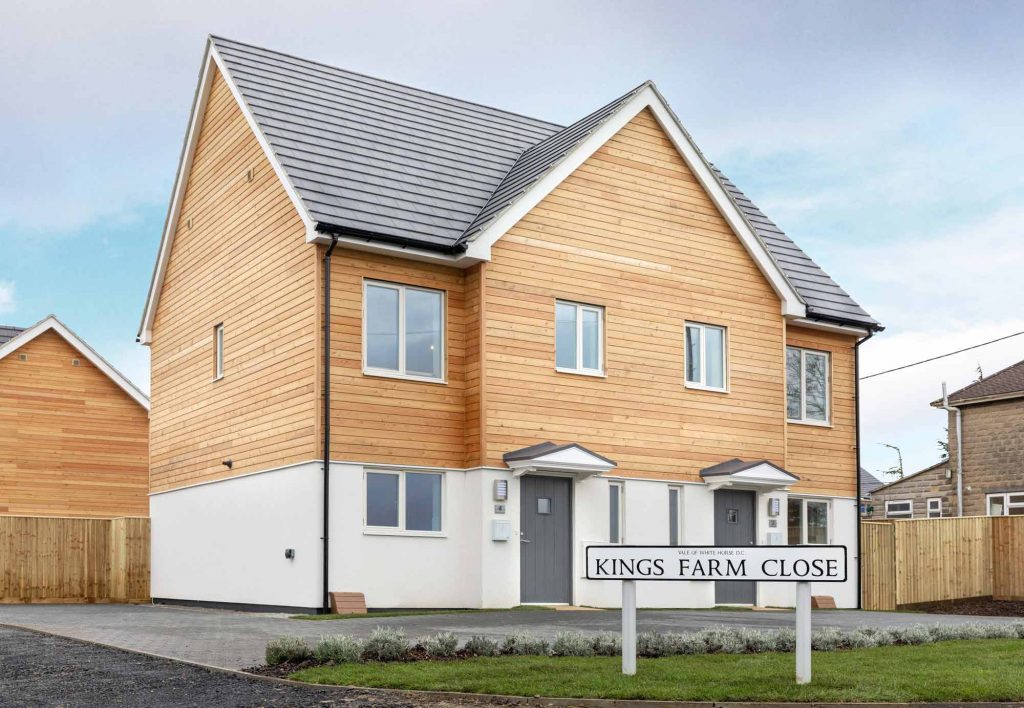
One such development currently under
construction is Kings Farm Close. A collection of 15 new homes on the outskirts
of the Oxfordshire village of Longcot, the development promises affordable,
sensitively designed dwellings fit for 21st century living.
More significant, however, is that Kings Farm
Close also claims to be the most sustainable housing development in
Oxfordshire.
Modern methods of construction
Ian Pritchett, managing director of
Oxfordshire-based Greencore Construction, has been championing a fabric-first
approach to new home building, using eco-friendly, modern methods of
construction for some time. His approach is to build to the highest standards while
also delivering comfort and quality at a great price.
Every Greencore home is built offsite in a
factory using a timber frame panel system, which is insulated with a mix of
hemp, lime and wood fibre. The hemp-lime mix provides exceptional levels of
thermal performance – tests carried out by Bath University showed that this
system stores nearly four times the amount of heat when compared with
traditional insulation materials like mineral wool.
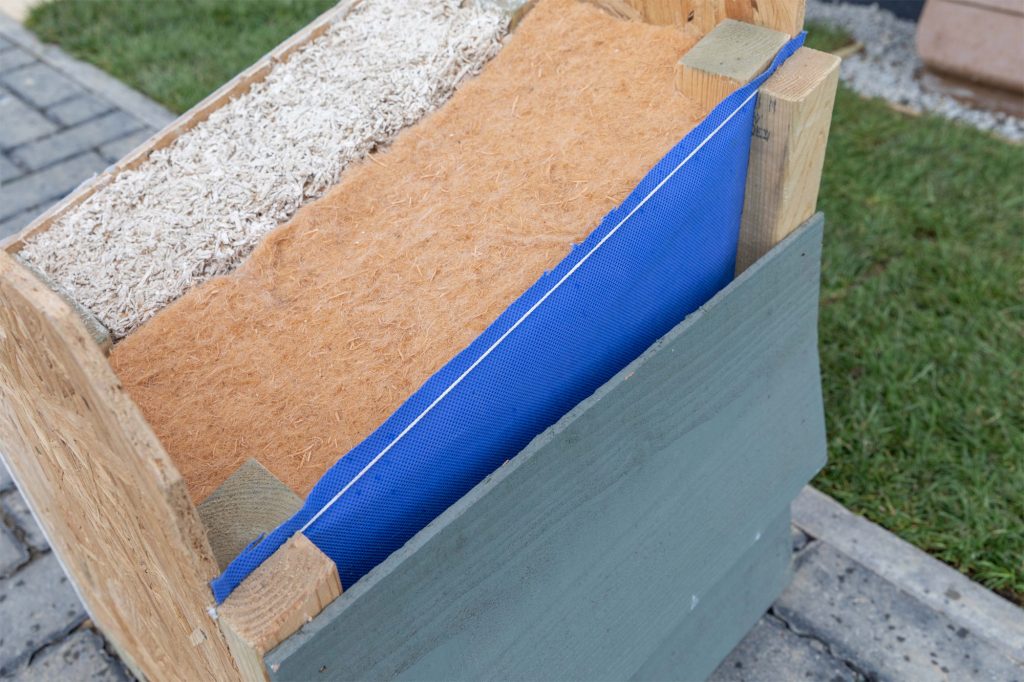
Meeting the double carbon target
This insulated panel system – branded as the
Biond Building System – is manufactured almost entirely from natural materials.
It means that Greencore’s homes, which are always built to Passivhaus thermal
performance standards, can achieve the double carbon target of a low carbon
footprint and low operational energy usage.
Ultimately, it means the homes’ occupants won’t
need to use their heating as often. This is because the hemp-lime and wood
fibre insulation in the superstructure – and a mechanical ventilation and heat
recovery unit – help to maintain a comfortable indoor temperature all year
round. The heating is provided entirely by underfloor heating, leaving wall
spaces clear for furniture and decoration.
So, how is this possible? How does a humble
plant-based insulation material like hemp-lime make such an impact on the
thermal performance of a home?
Hemp-lime ‘phase change’ properties drive thermal efficiency
It’s all thanks to the natural ‘phase change’
properties of hemp-lime. The moisture naturally present in the cells of the
hemp and in the pore spaces of the composite material can change from liquid to
vapour and back again. When this change takes place, a lot of energy is either
absorbed or released.
This phase change process can take place at a
wide range of temperatures and means that energy entering or leaving one face
of a wall is very different to the energy entering or leaving the other face.
The reality is that the combination of good insulation and exceptional thermal
inertia resulting from the natural phase change properties makes hemp-lime an
extremely high performing material.
A little hemp-lime history…
Hemp-lime has been used as a building material
for hundreds of years in central Europe, but was revived in the 1990s in France
as a niche construction technique for new houses and for infilling the panels
of historic oak-framed buildings.
The new-build technique involves casting a wet
mix of hemp and lime around a timber framed structure to form solid monolithic
walls, normally finished with a lime render on the outside and lime plaster on
the inside. This form of building has gained popularity in France and spread to
the UK in the early 2000s.
Avoiding the delay of drying wet hemp-lime
Despite its rise in popularity, one major
limitation hampers the use of wet cast hemp-lime in volume construction
projects: it takes a long time to dry. In ideal weather conditions (warm, dry
and breezy), drying can take as long as six to 12 months, which clearly isn’t
practical for fast-track housebuilding in unpredictable British weather.
To tackle this, Greencore pre-fabricates the
superstructure of each home at its factory – ready-filled with hemp-lime and
wood fibre insulation – before it’s shipped out to be assembled onsite. This
means the drying process can be managed in a controlled, indoor environment.
Once on-site, the superstructure of each building can be erected in a matter of
days. It’s modern methods of construction with a natural, sustainable twist.
Taking sustainability to the community
For Greencore and its partners, however, the
sustainability focus doesn’t stop with the homes themselves. Back at Kings Farm
Close, developer Oxford Advanced Living (OAL) – with support from affordable
housing provider Sovereign – has made a concerted effort to build
sustainability into the very fabric of the community.
“A fifth of the site’s total area will be
shared green space,” says Martin Pike, director of OAL, “planted and managed
with native trees to support wildlife under a biodiversity plan. This project
has really allowed us to put into practice all our ideas and determination to
create a genuinely sustainable community in Oxfordshire.”
With 40% of the development given over to
affordable housing, Greencore and OAL are keen to champion a ‘sustainability
and quality for all’ approach to housebuilding.
“With these homes, the same high performance
standards are available to everyone, regardless of whether you’re renting or
buying a home,” says Martin. “We believe that all the residents will be able to
enjoy greener and healthier lifestyles at Kings Farm Close, and we intend to
work closely with them to help us with future projects.”
Alex Brooks, development manager at Sovereign,
agrees. “These new affordable homes will not only be great places to live,
they’ll also be good for the environment as well as keeping energy bills low
for residents. It’s really important that we build homes and invest in
communities that are fit for the future.”
Support from MPs
It’s an approach that hasn’t gone unnoticed in
political circles, either. In March this year, Ed Vaizey, the former culture
minister and MP for the Oxfordshire constituency of Wantage, took time out of
his schedule to visit Kings Farm Close and see the project first hand.
“The vast majority of new-build homes in the
UK are of bland design, poor build quality and lack basic sustainability
credentials,” he says. “Much of this is to do with national housebuilders
refusing to embrace new technologies and construction methods.
“The Kings Farm Close development, however, is
a shining example of forward-thinking, modern housebuilding from a team of
people who are clearly very committed to bringing sustainable living to
everyone – whether you own, part-own or rent your home.”
Recognition from sustainability leaders
In October 2018, Kings Farm Close was
recognised by sustainability charity Bioregional for its national leadership in
implementing One Planet Living, a comprehensive framework for planning, building
and managing greener communities.
Nicole Lazarus, head of Bioregional
Oxfordshire, praised the development, saying: “The Kings Farm Close team richly
deserve recognition for their leadership in creating the kind of sustainable
new housing we need so badly. We particularly love the natural materials used
in the build system and the high-quality indoor environment that they make
possible.”
There’s a lot to be said for the power of
plant-based materials in construction. The fact is the more of these materials
we incorporate into buildings, the more carbon we lock up – plain and simple.
Recent industry data shows that the
construction of an average house produces 50 tonnes of CO2. On the
other hand, construction of a Greencore home, using the hemp-lime timber frame
panel system, produces very low or zero CO2 in the construction
process.
With construction work at Kings Farm Close
expected to complete in the autumn of 2019, it won’t be long before the final
residents move in and the claim of ‘Oxfordshire’s most sustainable housing
development’ can be put to the test.
Comments are closed