How To Choose The Right Cement For Your Construction Project
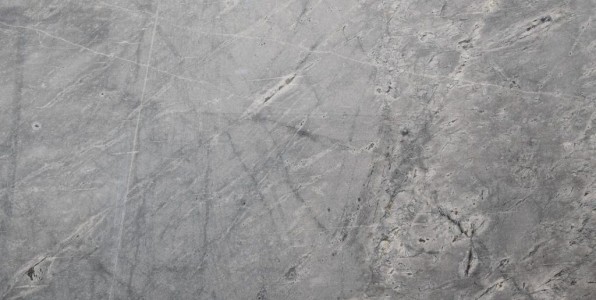
How To Choose The Right Cement For Your Construction Project
The post How To Choose The Right Cement For Your Construction Project appeared first on UK Construction Blog.
Cement is one of the most versatile and important components of any construction project. No matter what you’re working on, building strong and stable structures and foundations is a crucial part of the job at hand. And choosing the right cement is equally as important in ensuring the strength, durability, and longevity of that structure.
Cement is the binder that holds together sand, stone, gravel and other aggregates to form products like concrete or mortar. There are several types of cement, concrete and mortar, each with their own qualities, advantages and disadvantages, and choosing the right product can have a significant impact on the quality and appearance of the finished product. This blog will outline some differences between cement, mortar and concrete, the different types of cement, and some additives and dyes that can enhance their performance and aesthetic.
What’s the difference between cement, concrete and mortar?
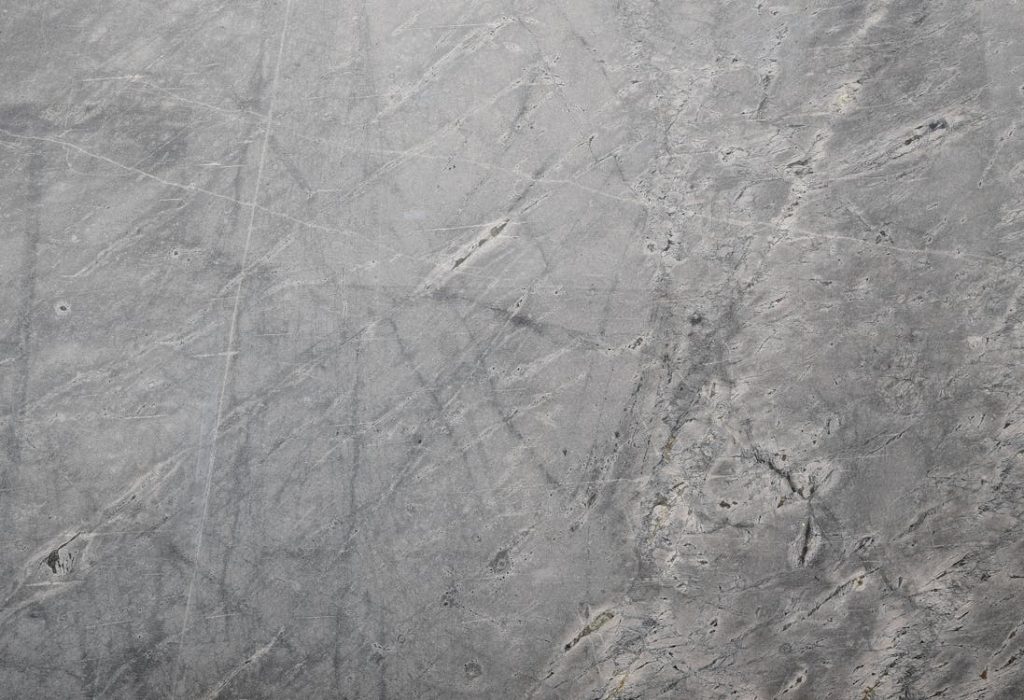
Sometimes these terms can be confused as the same thing, but cement, concrete and mortar are three individual materials with different qualities and purposes.
Cement
Cement is a fine powder used as a binding agent in several construction applications. It’s created from raw materials such as chalk, clay and limestone and mixed with metals and minerals such as aluminium, iron and calcium. A versatile material used to make concrete, mortar and screeds, cement is mixed into a paste and left to harden over time. There are several different types that are readily available across the country, including ready-mixed cement. Â
- Ordinary Portland Cement: This is the most popular cement when creating concrete and mortar mixes. Made of limestone, clay and gypsum powder, Ordinary Portland Cement (OPC) is available in different grades depending on qualities like strength and heat resistance. It’s perfect for many general-purpose construction jobs such as foundations, walls, floors and roofs because of its excellent durability and strength – so if you’re repairing a wall, building a driveway or creating a foundation for an outbuilding, shed or greenhouse, Portland cement is a great option.
- Portland Pozzolana Cement: This is created by mixing ordinary Portland cement with a pozzolana clinker and sometimes gypsum or calcium sulfate. Portland Pozzolana Cement (PPC) has a higher resistance to chemical reactions in concrete than ordinary cement and is often used in underwater concrete projects, bridges, dams and sewage works.
- White Cement: This is a type of ordinary Portland cement that has a distinct white colour because of the addition of iron and magnesium. It’s usually chosen because of its aesthetic value, helping to provide a bright, tidy decorative finish for pre-cast panels and exterior elements such as columns, mouldings, balusters and cornices.
- Rapid-hardening Cement: This cement has a quicker strength development process, meaning it will reach a higher strength rate quicker than ordinary cement. Rapid-hardening cement might have a higher lime content and will be a finer powder than normal cement.
- Quick-setting Cement: Unlike rapid-hardening cement, which develops a higher strength rate quicker, rapid-setting cement will have a faster setting time – it will harden faster, but still has a similar grain and strength rate to ordinary cement. Fast-setting cement is ideal for time-sensitive projects or jobs near water.
- Low-heat Cement: This cement is specially formulated to have a lower heat of hydration in concrete. Low-heat cement is a smart choice for larger concrete construction projects where controlling the temperature is important to prevent cracking.
- Sulfate-resistant Cement: This helps to reduce the side effects of sulfate on concrete, such as in foundations constructed in soil that has a high sulfate content.
These are just a handful of different types of cement, and there will be many other specialist options to choose from depending on the job at hand.
Concrete
Concrete and mortar are the two main products that can be created from cement, when it is mixed with water and other aggregates. Concrete is a mixture of cement, sand, water, minerals and chemicals. There are many distinct types of concrete but the three main types other than ordinary concrete are high strength, fast-setting and crack-resistant.
- Normal Strength Concrete: This is ordinary concrete that can be used for many general construction projects such as pathways or buildings where high strength isn’t needed.
- High Strength Concrete: This is a concrete that is exceptionally strong and can withstand high pressure. It’s ideal for heavy-duty constructions, foundations and bases but has a longer setting time than normal concrete.
- Crack-resistant Concrete: Designed to be especially long-lasting and durable, crack-resistant concrete reduces the risk of cracking or shrinkage when the concrete is setting. It’s perfect for patios and paths where there might be a lot of foot traffic.
- Fast-setting Concrete: This concrete hardens quicker than normal, which is great for more time-sensitive jobs.
Mortar
Mortar is a material often used in masonry construction projects – it’s the glue that binds together bricks, blocks and stones to form a solid, stable structure. A mixture of cement, sand and water, mortar holds walls and other structures in place and can even add aesthetic value with certain finishes and styles.
Masonry cement is a type of cement mix specially formulated for masonry applications and is primarily used for mortar. It contains a mixture of Portland cement and ground limestone, as well as additives such as lime, air-entraining agents or water-repellent agents to further enhance the workability or water retention of the mortar.
Cement additives and dyes
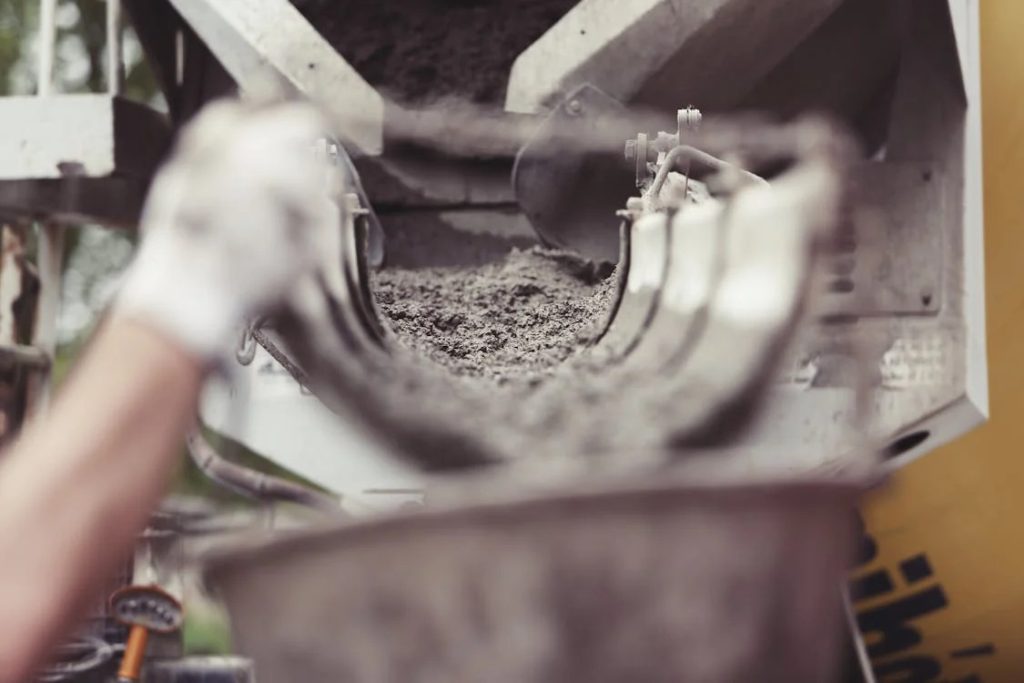
As well as considering the wide range of several types of cement available, there’s extras you can add to your cement mixes to achieve certain results. As well as minerals, you can add several chemical additives to improve the strength, durability or workability of your cement.
- Plasticisers: This loosens up your cement mixture, making it more flexible and easier to work with.
- Accelerators: If your project is time-sensitive, accelerators can be added to cement to speed up the setting time.
- Retarders: The opposite of an accelerator, this will slow down the setting time.
- Frost-proofers: This provides protection against frost and cold weather during the setting process.
- Waterproofers: This provides water-resistance to the cement which is helpful if you’re working in rainy or wet conditions.
- Hydrated Lime: This is a great additive for workability and flexibility and is often used in bricklaying and rendering.
- Dye and colourants: If you want your cement to be a specific colour, for example if you’re matching it to some existing cement, you can add dyes to the mix.
So, how do you choose the right cement for the job?
Consider the requirements of your project: What level of strength does your cement need? Does the setting time need to be fast or slow? What kind of environmental conditions are you working in? Do you need it to have a certain finish or colour?
After understanding the different types of cement, the differences between cement, concrete and mortar, as well as all the additives available to you, you should be able to decide which cement is right for the job you’re working on.
Comments are closed